Fazendo um Enxó Goiva
Neste vídeo, mostro a fabricação artesanal de um Enxó Goiva forjado em nossa oficina, a partir de uma barra redonda de aço SAE 5160. Projeto original do livro “Tool Making for Woodworkers”, de Ray Larsen. No livro, o autor oferece quatro projetos de ferramentas de entalhe, incluindo uma goiva para tornearia, um bedame e um formão oblíquo (skew chisel). Larsen dedica grande parte do conteúdo explicando as técnicas de fabricação, o que também faz do livro um ótimo manual, além de ser único no tema.
Filed under: Sem categoria | Leave a Comment
Entrevista com o Professor Tarcísio Mady, para o canal “Conhecendo a Madeira”.
Filed under: Sem categoria | Leave a Comment
Mesinha-banco Maria
Projeto original de Michel Arnoult, desenhado em 1998. Após seu falecimento, sua filha, Annick Arnoult, encontrou uma mala com projetos inéditos de seu pai. Entre estes projetos, Annick escolheu a mesinha-banco Maria, e em nossa oficina-escola realizamos a sua construção. Uma honra poder participar de um projeto inédito do nosso designer Michel Arnoult. Confira as fotos do processo de fabricação no vídeo.
Para saber mais sobre Michel Arnoult, acesse:
Filed under: Sem categoria | 1 Comment
Construindo com Alvar Aalto
Criador de ícones da arquitetura e do design modernos, o finlandês Alvar Aalto foi um dos pioneiros na fabricação seriada de móveis compostos a partir de um plano bidimensional, conformando peças curvas feitas de madeira laminada. Formas sinuosas e orgânicas exibem a plasticidade da madeira em móveis racionais e de poucos elementos.
Neste artigo, apresento o projeto desenvolvido pelo designer Thiago Pires, aluno do curso Coisas de Madeira, elaborado a partir de imagens da poltrona 402, de Alvar Aalto. Exercício com propósito didático, tratou-se de uma experimentação das possíveis técnicas de construção em oficina convencional.
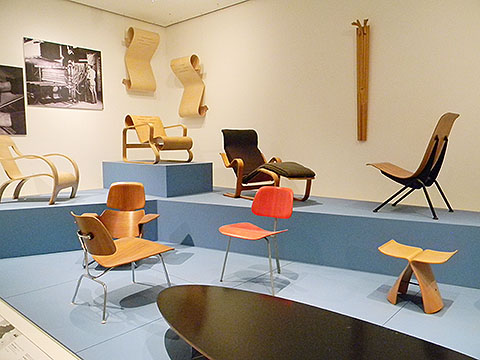
Exposição de mobiliário de madeira laminada, diversos autores. MoMA, 2013
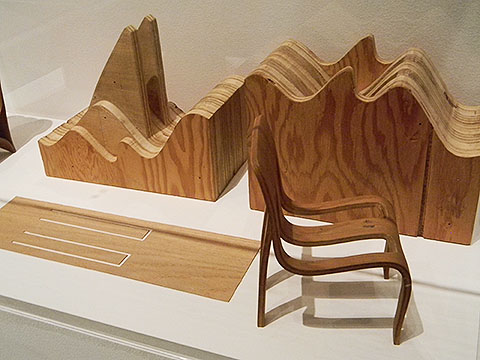
Modelo de cadeira, molde e folha de madeira compensada. Peter Danko (norte-americano, 1949). MoMA, 2013
Hugo Alvar Henrik Aalto (1898 – 1976)
A cadeira Paimio, provavelmente a mais conhecida peça de mobiliário projetada por Aalto, leva o nome da cidade localizada no sudoeste da Finlândia, para a qual projetou um sanatório de tratamento de tuberculose, incluindo os seus móveis. A estrutura da cadeira consiste em duas alças fechadas de madeira laminada, formando braços e pernas, e o assento numa folha delgada de compensado curvado em forma de pergaminho. Foi inspirada na cadeira Wassily, de Marcel Breuer. Para esta cadeira, Aalto escolheu a madeira de bétula, espécie nativa notável por sua elasticidade e seu belo aspecto natural.
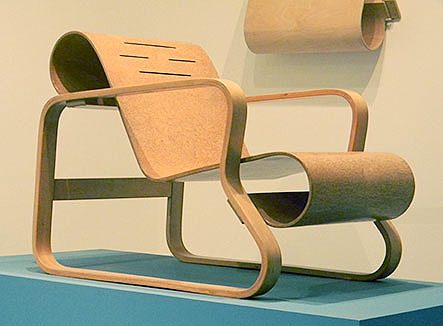
Cadeira Paimio, 1931 – 32. MoMA, 2013
Esta cadeira foi cuidadosamente projetada para atender aos pacientes do sanatório, que convalesciam de problemas respiratórios. Leve e resistente, foi uma das protagonistas da produção seriada de peças de madeira laminada e curvada.
Em 1935, a empresa Artek foi estabelecida na Finlândia para distribuir móveis de madeira projetados por Aalto e sua esposa, a arquiteta e designer Aino Aalto. A maioria de seus projetos permanece em produção.
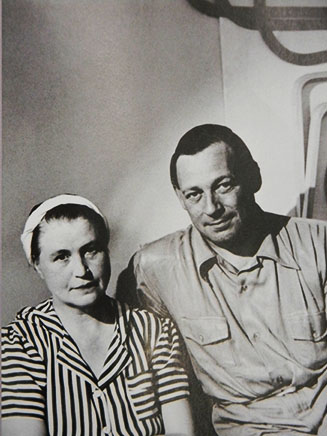
Aino e Alvar Aalto
Seu design influenciou artistas como o casal norte-americano Charles e Ray Eames, que por sua vez também criou um importante repertório de móveis de madeira laminada.
Na oficina
Este projeto teve dois momentos principais: a construção do modelo e a construção do protótipo. O modelo foi confeccionado em escala natural, de compensado. Serviu para confirmar e reajustar as informações previstas no desenho técnico, como a sua ergonomia e demais medidas.
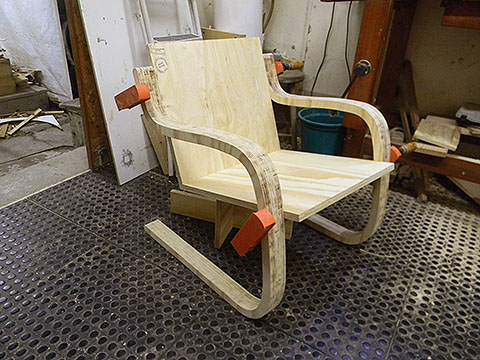
Modelo de compensado.
E antes de iniciarmos o protótipo, foi preciso construir uma fôrma para modelar as laterais (arcos) da poltrona. A precisão do encaixe das peças positivo/ negativo é determinante em relação à qualidade da peça modelada, não podendo haver frestas entre as lâminas durante colagem, o que comprometeria todo o trabalho.
Originalmente, as cadeiras com peças laminadas de Aalto são de bétula (betula spp), madeira flexível, natural na Finlândia e em diversas regiões do hemisfério norte. As espécies de clima tropical não são tão adequadas para este propósito como as de clima temperado, por isso não encontramos boas madeiras no comércio brasileiro. Optamos pelo tauari (couratari spp), por recomendação de algumas fontes bibliográficas. O tauari possui grã direita, boa conformação e aspecto uniforme, o cerne é praticamente isento de nós e oferece excelente colagem.
Uma importante condição é que os cortes sejam radiais – perpendiculares aos anéis de crescimento -, o que garante mais resistência da fibra ao curvar a lâmina. Manter a ordem das lâminas também garante a retidão das peças conformadas.
As lâminas foram extraídas de um pranchão, com aproximadamente 40 cm de largura. Ao final, tivemos uma incrível perda de 2/3 do volume total, devido ao número de cortes. Cada lâmina obteve 2 mm ao final do aparelhamento, passando também pelas plainas. Precisamos utilizar 15 lâminas, um número maior em comparação a original, que utiliza apenas seis lâminas, pois o tauari, embora resistente, é madeira pouco flexível.
Conformação dos arcos
Com a fôrma e lâminas de tauari prontas, iniciamos a colagem das lâminas. Antes fizemos um ensaio, conformando as lâminas sem cola, assim pudemos estimar o tempo para esta operação, limitado pela secagem da cola. Utilizamos cola de alta secagem, a cola vinílica Titebond III. Outra opção seria utilizar cola de uréia-formol, que proporciona ótima cristalização da cola. Embora a Titebond seja uma cola vinílica, colas brancas em geral não são recomendadas, pois não oferecem rigidez suficiente às peças sob pressão. Podem funcionar num primeiro momento, mas em pouco tempo a colagem pode ceder.
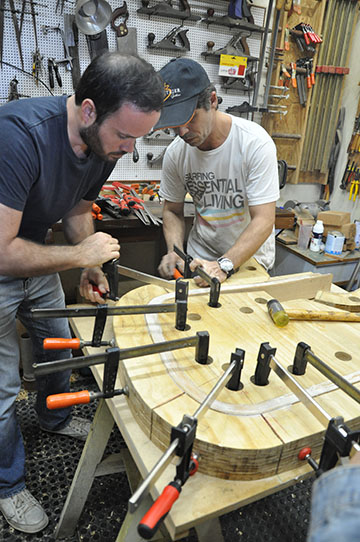
Foto: Marcos Husky
Precisamos de pouco menos de 30 minutos para conformar cada peça. Para espalhar a cola, acomodamos cada lâmina numa calha de compensado, onde recebia a quantidade exata de cola com uma espátula.
A cura total se dava após alguns dias, devido a grande quantidade utilizada. Para cada peça aplicamos 1/2 litro de cola.
Vídeo: Marcos Husky
Depois das peças secas, as bordas foram retificadas. A primeira borda com plaina manual, e a borda posterior com serra-circular.
A raspilha serviu para retirar as marcas das faces e resíduos de cola. Eventuais marcas de grampos, onde a peça foi amassada, utilizamos um ferro de passar roupas sobre um pano úmido. Assim, a madeira dilata e retorna à superfície.
O encosto/ assento
Estrutura montada com madeira de pinnus, foi preparada para receber estofamento, com percintas sob o assento. Antes de grampear as percintas, experimentamos sua eficiência num quadro feito de compensado. O quadro deformou, mostrando a enorme força de tração das percintas. Por isso, além de reforçar esta estrutura com cantoneiras, utilizamos boa espessura em suas peças.
Sobre o encosto e o assento, experimentamos espumas de várias densidades, suficiente para não “afundar” ao sentar. Na busca do melhor conforto, testamos a cadeira e seus possíveis usos…
Para a união das pernas com o assento, utilizamos parafusos com porcas americanas, embutidas nas pernas. Em cada ponto de fixação aplicamos um par, o que garantiu resistência suficiente, possível desmontabilidade e discrição, pois não há o que indique a união nas partes externas. Este é um dos “segredos” desta poltrona.
A exemplo das poltronas de Aalto, utilizamos percintas cruzadas no assento. Devem ser bem tracionadas, com grampos fixados na diagonal, como mostra a foto.
O estofamento
Sobre todo o conjunto aplicamos uma fina camada de acrilon, e cobrimos o conjunto com tecido tipo sarja. Depois de alinhavado, as costuras foram fechadas em máquina. As bordas foram grampeadas, e o tecido esticado por baixo do assento. Para isso, durante a montagem da estrutura, foi deixada uma fresta de 10 mm para permitir a passagem do tecido, como mostra a foto.
Montagem e acabamento
Sobre as peças de tauari utilizamos óleo de Tungue, resultando num tom acetinado e natural. Algumas demãos devem ser aplicadas até a superfície da madeira saturar. Depois de seca, a madeira foi polida com um pano limpo de algodão.
Uma fina placa de compensado revestida com sarja foi parafusada nas costas da poltrona, sendo esta a última ação deste expediente.
O resultado não poderia ter sido melhor. Extremamente confortável e com a belíssima estética de Alvar Aalto, um dos artistas mais brilhantes do séc. XX.
Este trabalho não teria sido possível sem a iniciativa do nosso designer e aluno Thiago Pires. Contribuiu para este artigo nosso amigo, o arquiteto e designer Marcos Husky, e Tommy Mac, com seus vídeos, onde mostra importantes dicas para a conformação de peças curvas laminadas. Demais fontes:
https://www.artek.fi/en/company/about
Clique para acessar o Chai41_CristineSayuri.pdf
https://craftcouncil.org/magazine/article/bent-design
http://www.finlandia.org.br/public/default.aspx?contentid=124168
https://www.moma.org/collection/works/4407?artist_id=34&locale=pt&page=1&sov_referrer=artist
http://www.ipt.br/informacoes_madeiras/3.htm
Bibliografia
Woodbending handbook / W. C. Stevens & N. Turner. East Petersburg, PA: Fox Chapel publishing, 2008.
Woodworker’s guide to bending wood / Nonathan Benson. East Petersburg, PA: Fox Chapel publishing, 2008.
Tage Frid Teaches Woodworking, book 2. Taunton Press, 1981.
Madeiras para marcenaria, carpintaria e artesanato / Antonino Tripodi. São Paulo, CTT Cultural e editora, 2006.
A madeira e seus usos / Júlio Eustáquio de Melo e José Arlete Alves Camargos. Brasília: SFB/ LPF/ MMA, 2016.
Coleção Folha Grandes Designers. Aalto, Alvar / Licenciado por AUTVIS, Brasil, 2012.
ATENÇÃO
Diversos procedimentos de oficina oferecem riscos. Por isso devem acompanhar o uso de EPI (Equipamento de Proteção Individual): óculos de proteção, máscara contra pó, protetores auriculares, entre outros dispositivos de segurança. Apenas pessoas capacitadas devem operar máquinas e ferramentas de corte; ao contrário estarão sujeitas a graves acidentes.
Filed under: Sem categoria | 1 Comment
Há alguns anos, passeando na feira de antiguidades da Praça XV, Rio de Janeiro, achei uma serra de costa que chamou de longe a atenção pelo belíssimo desenho de seu punho. No entanto, o estado do serrote era deplorável, mas por um preço bem razoável o levei para uma possível restauração. Recentemente tenho investindo mais nas serras da nossa oficina, e resolvi também dar uma oportunidade para esta velha serra e integrá-la em nosso expediente.
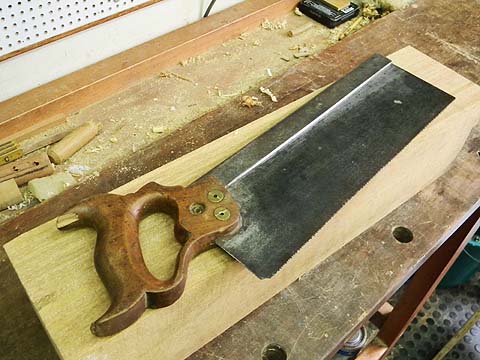
A serra de costa antes da restauração.
Neste artigo mostro a restauração de uma serra de costa da marca inglesa Spear & Jackson, do tipo tenon saw. Possui 14″ de comprimento (35,5cm), que serve para trabalhos de marcenaria em geral, devendo produzir cortes de precisão.
Spear & Jackson
“As raízes da Spear & Jackson datam a partir de 1760, quando o fabricante de cortinas John Love decidiu fundar uma empresa de produtos de aço em Sheffield, Inglaterra, onde a produção de aço, talheres e ferramentas estava concentrado devido a abundância de matérias-primas. Ele associou-se com Spear Alexander, um rico comerciante da cidade vizinha de Wakefield, e a nova empresa recebeu o nome Spear & Love.
Nas décadas seguintes, a empresa passou a se concentrar na produção de serras, e os negócios cresceram. Em 1814, a empresa passou a ser administrada pelo sobrinho de Spear Alexander, John Spear, que, por sua vez, trabalhava com um assistente chamado Sam Jackson. Jackson mostrou ser um notável profissional, e em 1830 associou-se a empresa e esta foi renomeada Spear & Jackson.”
A empresa continua a produzir serras e outras ferramentas até os dias atuais, associada a diversas outras marcas conceituadas.
Fonte: http://www.tfsrcymru.org.uk/wp-content/uploads/2013/01/Spear-Jackson-history-and-billhook-types.pdf
Ao longo dos anos, a Spear & Jackson fabricou serras associada a diferentes marcas. Esta serra apresenta a marca “Laep-Frog”, provavelmente uma das marcas de melhor qualidade associada a Spear & Jackson. Encontrei no “Catalogue of Saws and Tools, Spear & Jackson, 1923”, a serra de costa nº 46 da marca “Leap-Frog”, idêntica na descrição e no desenho do punho.
“Esta serra corresponde em qualidade com a nossa serra manual nº 24, e é a principal e mais versátil serra do carpinteiro.” O catálogo está disponível para download no site do meu caro amigo Wictor A. Kuc, editor da revista WK Fine Tools:
Início da operação
O serrote estava muito danificado, com um dos “chifres” do punho quebrado, com a lâmina empenada e severamente enferrujada, dentes deformados, com marcas profundas da ação do tempo e do mau uso.
Este tipo de serrote tem porcas chatas e redondas, conectadas aos parafusos que fixam o punho na lâmina. Li diversos artigos sobre as dificuldades de desmontar este tipo de serrote, com o risco principal de quebrar estas porcas. Ademais, são difíceis de encaixar uma chave em sua fenda, pois são rasas, provavelmente em virtude do fabricante ter faceado o punho com as porcas instaladas. Por isso é necessário avaliar se há a necessidade de desmontar o serrote para restaurá-lo. Este era o caso, devido aos variados danos que apresentava.
Com uma chave improvisada retirei as porcas sem dificuldades. O problema foi retirar os parafusos, que estavam engatados. Mais tarde reparei que os furos da lâmina são precisamente do diâmetro dos parafusos, e qualquer desvio impossibilitaria o seu encaixe. Pois bem, os parafusos estavam todos empenados. Para retirá-los precisei empurrar os parafusos com martelo e repuxo, o que inevitavelmente acabou ferindo o passe e danificando o encaixe com as porcas. Por conseqüência as porcas ficaram inutilizadas, o que me obrigaria a usinar novas porcas.
A lâmina
Estava empenada no sentido longitudinal e transversal, encanoada e torcida. Não sei como é possível deformar tanto uma lâmina com a qualidade deste aço. Para desempená-la utilizei um cepo de cumaru com a face reta para deitar a lâmina e um martelo-bola. Golpeei a lâmina rapidamente e com leveza, espalhando os golpes sobre a face convexa, sempre verificando a retidão com o auxílio de uma régua.
Lâmina resiliente, precisei repetir o trabalho algumas vezes durante o restauro, como se fosse a afinação das cordas de um piano. Desempená-la com as mãos, tentativa inútil. Realmente é impressionante a qualidade deste produto, reconhecido pela especial constituição de seu aço.
Os dentes da lâmina estavam completamente disformes e desalinhados. O último sujeito que tentou afiar esta serra o fazia de qualquer maneira. Não havia como recuperar os dentes, por isso retirei-os com uma lima chata, transformando a lâmina numa régua perfeitamente reta.
Para reformar os dentes utilizei uma serra de costa de 12PPI (11TPI) para servir como gabarito e orientar a lima. Juntei as lâminas e com uma lima triangular fina marquei a lâmina sem dentes. Precisava apenas desta marcação para iniciar a sua reforma.
O segredo para conseguir fazer 160 dentes iguais, senão bem parecidos, é trabalhar o conjunto dos dentes. Apenas para a reforma dos dentes atravessei a lima quatro vezes por toda a lâmina, e a cada passagem deslizava duas ou três vezes a lima, não mais.
Tinha três preocupações para cada golpe de lima:
- Manter a lima a 90º nos eixos x, y e z;
- Manter a face superior da lima ligeiramente deitada a 20º;
- Deslizar a lima duas ou três vezes para frente, sem arrastá-la no retorno. Iniciar o exercício a partir do topo da lâmina em direção ao punho.
Para saber sempre qual dente era limado, marquei os dentes por cima com caneta Pilot; assim, a cada passagem retirava a marca da caneta. Na reforma dos dentes os golpes de lima são seguidos, um dente após o outro. Para desgastar a lima de maneira uniforme é importante girá-la durante a operação, para utilizar todas as suas arestas. Por fim retirei a rebarba dos dentes deslizando uma pedra diamantada gramatura 600 nas faces da lâmina.
Uma ótima fonte de informações sobre afiação de serras está na pagina do mestre e designer Morito Ebine, em http://www.moritoebine.com/Afiacao%20Serrote.pdf
Limpeza do aço
Para retirar a ferrugem da lâmina e da haste de aço (costa), primeiro submeti as peças a um banho eletrolítico, técnica que explico no artigo “Os segredos de uma restauração“.
Uma vez lavadas as peças, utilizei lixas para metal, com graduações 100, 150, 220, 240, 320, 400, 600, e por fim pasta de polir. Utilizar um bloco de lixa evita o desgaste dos dentes, e também promove um lixamento mais uniforme. Utilizei querosene no lixamento, ajuda a mantê-las desentupidas por mais tempo. Essência de terebintina também é muito utilizado. No entanto é praticamente impossível retirar por completo as profundas erosões causadas pela oxidação, assim como as marcas produzidas pelo uso. É notável como a costa da serra era constantemente retirada, pelas marcas de martelo próxima às suas extremidades.
Apesar de ainda marcada pela oxidação, ao final obtive um ótimo polimento, o que contribui para o deslizamento da lâmina durante o corte. A haste da costa foi desempenada e recebeu o mesmo tratamento, com o cuidado de preservar as marcas estampadas.
Porcas e parafusos
Outra providência foi restaurar os parafusos e fabricar novas porcas. Para isso precisava desempená-los e refazer o seu passe. Com um cossinete refiz o passe dos parafusos, mas as porcas originais não serviam mais. Para refazê-las utilizei um torno para madeira e alguns parafusos de latão. A cabeça sextavada do parafuso de 10mm de diâmetro serviu perfeitamente, não poderia ser melhor.
Dediquei um bom tempo afinando o torno, para que a ponta-motriz e a contra-ponta se alinhassem perfeitamente. Uma vez ajustada a máquina, perfurei logo todos os parafusos. Primeiro marquei o centro com a ponta de uma broca curta, e em seguida perfurei a peça em etapas, pois a velocidade do torno para madeira é muito alta para usinar metais, e é fácil quebrar uma broca fina. Também é importante manter a broca constantemente lubrificada e resfriada com óleo fino durante a operação.
Para usinar a face e a borda utilizei uma lima velha como bedame. O latão não ofereceu resistência, e permitiu um trabalho extremamente preciso, no calibre do paquímetro. Para polir o metal utilizei apenas uma lixa de óxido de alumínio de graduação 240.
Com as peças ainda instaladas no torno fiz a rosca interna com um vira macho. Para fazer a fenda nas porcas, utilizei um gabarito para orientar a serra de arco. Após o corte das fendas, retornei os parafusos para o torno e finalmente separei as peças.
Para terminar, poli as cabeças dos parafusos e do medalhão. No medalhão utilizei o mais doméstico dos produtos abrasivos: pasta de dente. Deixou o medalhão polido e manteve o latão íntegro.
O punho
No punho, precisei redefinir a profundidade das novas porcas, corrigir a ponta quebrada do “chifre” com uma pequena emenda e dar um novo acabamento em sua madeira. Faia (beech) é a madeira original do punho, das madeiras mais comuns para toda sorte de serras manuais.
Lixado e remodelado o punho, aprofundei ligeiramente os escariados para encaixar as porcas, mais espessas que as originais.
Apliquei um tingidor cor mogno para uniformizar seu aspecto. Em seguida apliquei uma fina camada de seladora e encerei o punho, conferindo um aspecto acetinado e suave. Esta peça ficou como nova.
Lâmina, punho, haste, parafusos prontos. Após conferir o comprimento e a passagem dos parafusos, montei o serrote sabendo que seria uma única vez, pois os parafusos entrariam justos e retirá-los novamente poderia comprometer o seu passe.
Preferi primeiro montar o punho e a lâmina, para garantir o delicado trabalho de encaixe dos parafusos e, em seguida, encaixar a pesada costa de aço. Ok, sem problemas. Serrote montado, vamos afiá-lo.
Travamento e afiação
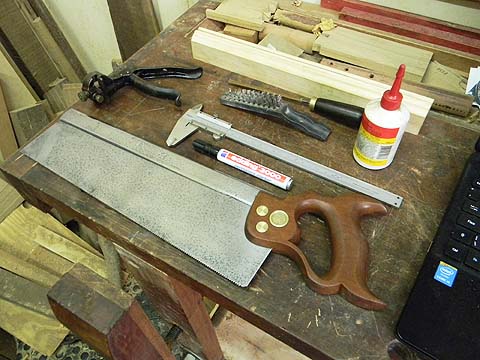
Ferramentas de afiação: alicate travador, lima triangular, pincel atômico e paquímetro.
Para este serrote fiz uma afiação comum, mais apropriada para cortes longitudinais, mas que também permite cortes transversais, resultando numa ferramenta versátil.
Primeiro providenciei a trava (desalinhamento dos dentes). O corte deve ter uma espessura pouco maior que a espessura da lâmina da serra, ao contrário, a serra pode prender durante o corte. Algumas serras dispensam a trava, quando se trata de cortes muito finos e superficiais. Ao final a trava ficou com 0,4mm a mais que a sua própria espessura de 0,6mm, resultando num corte de 1mm de largura.

Dentes travados.
Travados os dentes, procedo a afiação. Com a lima na mesma posição utilizada na reforma dos dentes, esta é passada agora de maneira alternada, apenas nos dentes que apontam para fora da lâmina. Assim, ora afia-se os dentes com a lâmina voltada para um lado, ora com a lâmina voltada para o outro lado. O cuidado com o alinhamento dos dentes deve ser constante.
Cortes ligeiros, limpos e retos em ambos os sentidos da madeira maciça, com pouca rebarba na saída do corte transversal. Devido a pesada costa deste serrote, ele exige prumo, bastando manter a serra equilibrada para gerar um corte reto. O punho abraça a mão, o que promove bastante firmeza durante o exercício.
Satisfeito com a nova ferramenta, tanto quanto fosse uma ferramenta nova!
– Diego de Assis
ATENÇÃO
Diversos procedimentos de oficina oferecem riscos. Por isso devem acompanhar o uso de EPI (Equipamento de Proteção Individual): óculos de proteção, máscara contra pó, protetores auriculares, entre outros dispositivos de segurança. Apenas pessoas capacitadas devem operar máquinas e ferramentas de corte; ao contrário estarão sujeitas a acidentes graves.
Filed under: Sem categoria | 11 Comments
Tage Frid no Brasil
Entre os projetos de marcenaria praticados em nosso Curso certamente este foi um dos mais sofisticados, na sua técnica de construção e design. Foi um grande desafio construir um móvel de Tage Frid; ser preciso e fiel ao projeto do início ao fim significou tempo e esforço, com momentos de resignação e muito trabalho. Tage Frid – ícone da marcenaria americana – utilizava técnicas variadas, tradicionais e modernas, o que proporcionava aos seus alunos condições para atuar em qualquer oficina. Seu design de estilo escandinavo é arrojado e não dispensa detalhes, devendo sempre ser bem resolvido na forma, na função e em suas proporções; segundo Frid, “Eu acho que a proporção – a relação correta entre as dimensões – é a coisa mais difícil de aprender. Muitos dos meus alunos têm o mesmo problema. Proporções inadequadas podem estragar um bom design.” (Tage Frid teaches woodworking – Furnituremaking, ed. Tauton, pg. 145)
Seguindo os passos deste velho mestre chegamos ao resultado satisfatório, de acordo com a descrição do seu projeto. Imaginamos o privilégio de quem o teve como professor.
Neste artigo mostro a construção do Banco de três pés (Three-legged stool) , projeto apresentado em seu livro “Tage Frid teaches woodworking – Furnituremaking, ed. Tauton, pg. 145 – 154“, exercício praticado com o aluno Eduardo Serra, arquiteto e marceneiro amador.
Tage Frid (1915 – 2004)
“Tage (pronuncia-se “Tay”) Frid era marceneiro, designer e professor, e também foi editor e colaborador da revista Fine Woodworking, desde a edição nº 1 a nº 171. É o autor da clássica série de livros Tage Frid teaches woodworking, publicado pela editora Taunton.”
Foto da contracapa do livro Tage Frid teaches woodworking, ed. Tauton.
“Nascido na Dinamarca, Frid foi aprendiz de um mestre artesão chamado Gronlund Jensen, iniciando em sua oficina aos 13 anos de idade. Cinco anos mais tarde recebeu o status de oficial (journeyman). Seguiu cursando arquitetura de interiores, enquanto trabalhava numa oficina de marcenaria com seu estilo dinamarquês moderno – a sua marca registrada. Em 1948 Frid mudou-se para os Estados Unidos, convidado para trabalhar como professor na School for American Craftsmen, primeiro em Alfred University e, posteriormente, no Rochester Institute of Technology. Então, em 1962 Frid lançou o primeiro programa de nível universitário em Marcenaria e Design de móveis em Rhode Island School of Design, onde sua influência floresceu para o próximo quarto de século.”
Fonte: http://www.finewoodworking.com/community/artistprofile.aspx?id=1094
O banco de três pés
Criada em 1982, originalmente feito de nogueira (walnut), Tage Frid construiu três versões da seu banco de três pés, modificando apenas o comprimento das pernas. No entanto, Frid condenava o design de bancos e cadeiras de três pés em geral, por oferecer riscos. Se uma pessoa sentada num banco de três pés inclina para um dos lados, este pode desequilibrar e tombar. Em seu design Frid evita esta falha, devido ao formato em “T” do seu assento: “O assento em forma de “T” contraria a tendência do banco de tombar, porque não existe área de assento na parte traseira para empurrar. O peso do corpo de quem senta está localizada sobre as duas pernas da frente, resultando num banco de três pés estável.” (Tage Frid teaches woodworking – Furnituremaking, ed. Tauton, pg. 145)
Foto do livro Tage Frid teaches woodworking – Furnituremaking, ed. Tauton, pg. 146.
Sentar-se com o encosto à frente também é uma opção, tão confortável quanto recostar-se. É levíssima e elegante, devido a sua extrema economia de material.
Na oficina
Escolhemos cedro (cedrela spp.) para construção deste banco, madeira leve e resistente, sempre “amigável” para os trabalhos de marcenaria. De forma geral, primeiro foram feitos os encaixes com as peças retas, e depois desta etapa cada peça foi modelada. Após o aparelhamento da madeira iniciamos sua construção conformando o assento em forma de “T”, com um encaixe de caixa e espiga. Tivemos um cuidado especial na marcação das peças, sempre considerando as perdas de material que haveria em sua modelagem.
Perfuramos o assento na furadeira de coluna, com seus devidos ângulos, testados anteriormente numa sobra de compensado. Em alguns momentos de sua construção utilizamos sobras para testar os encaixes, antes de executá-los nas peças – assim evitamos perdas desnecessárias.
Em seguida torneamos os pinos das pernas, para o encaixe no assento. Frid utiliza uma fresa para tornear estes pinos, instalada numa furadeira horizontal. Optamos por utilizar um torno, na falta da ferramenta sugerida.
Na união do encosto com o assento Frid utilizou um encaixe de rabo-de-andorinha (dovetail), garantindo extrema resistência. O ângulo entre o encosto e o assento é oblíquo, o que exigiu uma cuidadosa marcação.
Então fizemos os pinos do rabo-de-andorinha manualmente, utilizando serra de costa e formão para o entalhe.
Continuamos a confecção do rabo-de-andorinha na serra de mesa, inclinando a lâmina a 80º. A peça foi ligeiramente inclinada para trás, apoiada no batente preparado.
Em seguida conformamos a alça do encosto abrindo um furo na peça com a tupia de coluna, conduzida por um molde. A habilidade maior está na confecção do molde, onde a precisão é determinante para o resultado do trabalho.
Com a alça e o encaixe de rabo-de-andorinha prontos, terminamos o recorte do encosto na serra de fita, aproximando o aspecto final desta peça e da estrutura do banco.
Iniciamos a modelagem do assento conformando sua face côncava, utilizando primeiro a serra de fita para retirar a maior parcela de material, e depois a tupia de coluna para acertar o corte, conduzida sobre um gabarito.
Um complicador foi acompanhar a espessura irregular do assento, que aumenta em direção ao encosto a partir de sua borda frontal; assim como o encosto, o assento também possui a forma de cunha. Para este efeito inclinamos ligeiramente a peça, o que gerou um corte em forma de trapézio, como mostra a foto acima.
Trabalhamos primeiro a face côncava e depois a face convexa, garantindo nesta ordem a estabilidade da peça sobre a bancada em todos os momentos de trabalho. Utilizamos uma plaina curva #113 para acertar o corte da face convexa, uma outra opção para modelar as curvas do assento.
Antes de modelar as pernas do banco, marcamos os pontos de encaixe das travessas de acordo com suas posições e as perfuramos na furadeira de coluna.
Na serra de mesa iniciamos a modelagem das pernas, utilizando um gabarito para gerar a forma de cunha.
As pernas possuem uma seção elíptica. Para marcação das peças providenciamos um gabarito, recortado numa sobra de papel couro.
Marcamos as pernas e retiramos algum material com tupia, conforme sugere Frid nesta etapa do trabalho.
Com um rabote (plaina nº5) retiramos a maior parte de material. Para controlar este tipo de desbaste, convém primeiro conformar bordas retas e uniformes ao redor da peça, e depois retirar as arestas de forma gradativa. Em seguida utilizamos raspilha e lixas para sua finalização.
Após a modelagem das pernas pudemos fazer as travessas, últimas peças da estrutura do banco. Assim como as pernas, iniciamos com o torneamento dos pinos, cuidando constantemente de seu diâmetro durante o exercício.
Primeiro fizemos a travessa que une as pernas da frente. Recortamos a travessa na serra de fita, deixando a marcação bem visível para acertar o corte.
Desbastamos a travessa com um boxequim (spokshave), cuidando de sua simetria com um molde. Com esta travessa pronta conformamos a travessa perpendicular, semelhante em sua forma de fuso.
Montagem e acabamento
São quinze peças independentes que compõe o banco, considerando também suas cunhas. Para sua montagem primeiro conformamos o assento com o encosto, e por fim unimos as pernas. Utilizamos cola PVA em sua montagem.
Após a colagem e o acerto do rabo-de-andorinha providenciamos a união da caixa e espiga. Nesta ordem pudemos acertar antes as suas bordas; de outra forma – fixando todas as peças de uma única vez – não haveria passagem para acertos com a plaina manual.
Os pinos dos pés e das travessas são apertados com cunhas, que penetram num corte feito ao longo dos pinos. Fizemos estes cortes na serra de fita contra um espelho, para ver claramente o momento que a lâmina toca a peça.
Os pinos foram apertados no sentido longitudinal em relação à fibra da madeira do assento, como mostra a foto acima; assim se evita possíveis rachaduras. Após a secagem da cola as sobras foram serradas e acertadas com formão e lixas. As arestas foram retiradas, e todos os acertos necessários feitos. Pequenas fendas e furos foram tapados com massa acrílica no tom do cedro.
O acabamento foi feito com seladora e verniz à base de nitrocelulose, e polido após a secagem.
Trabalho concluído. Reproduzir o banco de três pés de Tage Frid foi muito gratificante, sendo possível apenas pela habilidade de alunos com maior experiência. A Eduardo Serra dirijo este crédito, e aos demais que crescem nesta oficina, criando boas histórias para contar!
– Diego de Assis
ATENÇÃO
Diversos procedimentos de oficina oferecem riscos. Por isso devem acompanhar o uso de EPI (Equipamento de Proteção Individual): óculos de proteção, máscara contra pó, protetores auriculares, entre outros dispositivos de segurança. Apenas pessoas capacitadas devem operar máquinas e ferramentas de corte; ao contrário estarão sujeitas a acidentes graves.
Filed under: Sem categoria | 1 Comment
Construindo Guerrit Rietveld
Reproduzir as cadeiras de Rietveld em nosso Curso de Marcenaria significa uma série de valores agregados, a começar por sua importância histórica – reproduzi-las é participar desta história. Por princípio técnico-didático, construir cadeiras constitui um exercício completo de marcenaria. De acordo com o comentário de Domingos Marcellini, “a cadeira é o móvel mais difícil de se fazer, não sendo dos mais modestos, pela suta e pela pouca largura das peças que a compõe.” (Manual Prático de Marcenaria, ed. Ediouro, pg. 158). No entanto Rietveld intencionava facilitar a reprodução, seja pelo processo de fabricação industrial ou artesanal, através de técnicas simples de marcenaria. Seus móveis minimalistas aparentam a estrutura como um objeto ao avesso, uma denúncia e um estímulo para sua construção – como é o caso de sua linha de móveis “Krat”, confeccionados com madeiras de embalagens. Suas ideias foram extremamente arrojadas à sua época, tornando-se ícones da movelaria contemporânea.
Neste artigo apresento as principais etapas do processo de fabricação das famosas cadeiras Vermelha e Azul e Zig-Zag, reproduzidas a partir dos projetos originais reunidos no livro How to construct Rietveld Furniture (de Peter Drijver e Johannes Niemeijer, ed. Thot), e a versão alternativa da cadeira Zig-Zag construída em compensado revestido.
Rietveld sentado em sua poltrona em frente à sua oficina (How to Construct Rietveld Furniture, ed. Thot, pg. 29)
Guerrit Thomas Rietveld (1888 – 1964)
Rietveld era filho de um marceneiro de Utreque (Holanda), e trabalhou na oficina de seu pai, onde adquiriu o conhecimento do ofício. Abriu em 1911 sua própria oficina de marcenaria, e mais tarde interessou-se também por arquitetura. Participou do movimento artístico holandês De Stjil (que literalmente significa “O Estilo”), fundado em 1917. O grupo baseava-se na “rigorosa precisão com que dividiam o espaço; pela tensão e pelo equilíbrio, alcançados com a assimetria; por seu uso das formas básicas e cores primárias; e pela máxima simplicidade de suas soluções.” ( Layout: o design da página impressa, de Allen Hurlburt, ed. Nobel, pg. 35). Rietveld procurou transformar as ideias do grupo a três dimensões; considerava indispensável que o mobiliário retornasse às suas formas básicas, como se os móveis nunca tivessem sido feitos. A cadeira deveria ser novamente concebida: deve ter seu assento, um encosto e algo que suporte estes elementos.
A cadeira Vermelha e Azul
Segundo Otakar Mácel, “a cadeira vermelha e azul de Guerrit Thomas Rietveld é reconhecida como o manifesto da estética De Stijl. Optando por formas simples, uma construção por módulos e recorrendo a cores primárias, este marceneiro de Utreque conseguiu criar uma peça de mobiliário moderna que personificava na perfeição os princípios estéticos do grupo neerlandês.”
Desenho original da cadeira Vermelha e Azul (How to Construct Rietveld Furniture, ed. Thot, pg. 24)
“Presume-se que a cadeira tenha sido criada em 1918, tendo em setembro de 1919 merecido destaque na revista De Stijl, em conjunto com a sua Cadeira de Criança. Ambas as cadeiras foram construídas com base no então recente método de aplicação de cavilhas, distinguindo-se a Cadeira Vermelha e azul pela sua forma mais simples e linear.”
“Os móveis de Rietveld dos anos 20 caracterizavam-se pela sua concepção de espaço muito própria e pela idéia de transparência, características que correspondiam aos ideais defendidos pela avant-garde funcionalista. O mesmo se aplicava à sua noção de produção industrial: Rietveld entendia que também a sua cadeira Vermelha e Azul podia ser fabricada industrialmente, na medida em que o material, as traves, as ripas e as tábuas podiam ser facilmente adquiridos no mercado e a construção não apresentava dificuldades maiores.” (Mobiliário Moderno – 150 anos de design, ed. H.F. Ullmann, pgs. 650, 651, 652).
Na oficina
Este exercício foi desenvolvido com o aluno Carlos Germano, oceanógrafo. Para a construção da cadeira Vermelha e Azul selecionamos maciços de freijó (cordia goeldina), madeira paraense extremamente versátil, própria para construção de cadeiras e móveis em geral. Originalmente o projeto sugere a faia (fagus spp.), gênero comum na europa para a construção de móveis.
Iniciamos o aparelhamento dos maciços com plaina manual nº5 e serra circular de mesa, conforme o padrão de medidas especificado.
Todas as peças da estrutura da cadeira são unidas com cavilhas de 15mm de diâmetro.Confeccionamos as cavilhas no torno, sendo necessárias vinte e duas unidades que, alinhadas, correspondiam a aproximadamente um metro de comprimento.
As peças foram cuidadosamente marcadas e perfuradas na furadeira de coluna, com broca Fostner. Os encaixes foram provados e marcados.
Para fixação das peças utilizamos cola PVA e grampos. É interessante notar que os grampos evitam a separação das peças por força da pressão hidráulica. Por isso as cavilhas prontas geralmente possuem ranhuras, o que facilita a expulsão do ar e do excesso de cola.
Uma vez conformada a estrutura, as peças do assento e do encosto foram recortadas na serra circular. Em princípio utilizamos compensado, mas mudamos para MDF, para obter uma cobertura com textura lisa.
Com cunhas fixadas sob o assento e o encosto, parafusamos estas peças.
Cobrimos o encosto e o assento com laca nitrocelulose, com o cuidado de revestir antes as bordas. Para a estrutura utilizamos verniz de nitrocelulose.
Achamos a combinação da estrutura em madeira aparente com os painéis coloridos tão atraente quanto a original. Então decidimos finalizar a cadeira nesta versão, a qual apelidamos de Vermelha e Azul e Freijó!
A cadeira Zig-Zag
Criada por Rietveld entre 1932 e 1934, a cadeira Zig-Zag foi composta com apenas quatro painéis maciços, fixados por parafusos combinados com encaixes de espiga e cunhas. Seu design também coloca em prática os mesmos princípios do movimento De Stijl, embora Rietveld tivesse rompido com o grupo em 1928. Suas linhas diagonais diferem da sóbria estrutura reta da cadeira Vermelha e Azul, cuja obra expressa os ideais do movimento De Stijl; a cadeira Zig-Zag é inquietante e instável – uma provocação aos sentidos.
Construída originalmente com maciços de carvalho (quercus spp.), em nosso curso de marcenaria optamos por versões em compensado revestido com folhas de freijó (cordia goeldina) e em maciços de peroba-de-campos (paratecoma peroba), de acordo com as dimensões do projeto original.
Versão original
Esta versão da cadeira Zig-Zag foi desenvolvida com o aluno Eduardo Acklas, produtor gráfico. Iniciamos a construção dos painéis aparelhando os maciços em pequenas tábuas, unidas com cavilhas e cola PVA.
Após o aparelhamento dos maciços, iniciamos a conformação dos painéis, cada um com três peças emendadas. Perfuramos as bordas com furadeira horizontal, e reforçamos a união com cavilhas.
Os painéis com emendas são mais estáveis; evitam o empenamento e rachaduras.
Com os painéis conformados e recortados, fizemos as espigas da união do assento com o encosto, utilizando a serra de mesa, com ligeira inclinação de 8º no batente do goniômetro, ângulo estabelecido para o encosto.
Em seguida fizemos os cortes das uniões do pedestal, com inclinação do disco de serra a 22,5º, cuja soma é igual a 45º.
Nas costas do encosto foi feito um pequeno entalhe para manipular a cadeira. Primeiro utilizamos a tupia de coluna para retirar o excesso de material, e em seguida terminamos o entalhe com formão e lixas.
Fizemos então as perfurações para a fixação de parafusos com porcas, utilizando a furadeira de coluna. É melhor escarear o maciço para o encaixe da cabeça do parafuso antes de transpassá-lo.
Na união do assento com o encosto encaixamos as espigas e utilizamos parafusos com porcas redondas.
Antes de unir os painéis do pedestal e do assento, foram fixadas cunhas como reforço. Utilizamos cola PVA, e os parafusos com porcas dispensaram o uso de grampos.
Acertamos as bordas com plaina manual. As superfícies e as arestas lixadas com lixas de grã 150 e 220. Acabamos a cadeira com seladora de nitrocelulose e cêra, conferindo o aspecto natural da madeira.
Versão em compensado revestido
Esta versão foi desenvolvida com o aluno Carlos Alberto Nery, psicólogo. Diferente da versão com maciços, o compensado é um painel pronto para ser recortado.
A união do assento e do encosto foi feito com encaixes em rabo-de-andorinha apenas, confeccionados com serra manual e formão. Fixamos estes painéis com cola PVA e grampos.
As demais uniões fizemos com parafusos Mittofix (auto atarraxantes); escareamos a cabeça dos parafusos e cobrimos os furos com massa acrílica.
O revestimento é ordenado; as partes internas são revestidas antes da união dos painéis, utilizando cola de contato. Aparentemente esta é a diferença entre a versão original e em compensado revestido – nesta versão os parafusos que conformam a união entre as peças ficam escondidos, sob o revestimento.
Assim como na versão anterior, o acabamento foi feito com seladora de nitrocelulose e cêra.
Assim testamos sua estrutura!
Aos meus alunos agradeço a oportunidade de realizar este trabalho, que retornou meu saudoso tempo como estudante de Desenho Industrial, tempo de descobertas e grande fascínio pelos móveis de Guerrit Rietveld.
– Diego de Assis
ATENÇÃO
Diversos procedimentos de oficina oferecem riscos. Por isso devem acompanhar o uso de EPI (Equipamento de Proteção Individual): óculos de proteção, máscara contra pó, protetores auriculares, entre outros dispositivos de segurança. Apenas pessoas capacitadas devem operar máquinas e ferramentas de corte; ao contrário estarão sujeitas a acidentes graves.
Filed under: Sem categoria | 1 Comment
na Amazônia paraense
Localizada próximo a Santarém (PA), na Reserva Extrativista Tapajós/Arapiuns, Surucuá é uma das sete comunidades ribeirinhas que participa das OCT – Oficinas Caboclas do Tapajós, projeto assinado pelo IPAM – Instituto de Pesquisa Ambiental da Amazônia. As OCT desenvolvem movelaria artesanal que expressa a cultura tapajônica, em bancos zoomorfos, no aproveitamento das formas naturais dos troncos e no uso de diversas espécies nobres de madeira, como a Sucupira amarela (Bowdicha nitida), o Jacarandá do Pará (Dalbergia spruceana), o Cumarú preto (Dipteryx odorata) e a Muirapixuna (Chamaecrista scleroxylon). A extração das madeiras é devidamente manejada e licenciada, e troncos mortos também são aproveitados.
Em fevereiro deste ano estive em Surucuá por uma semana, comunidade escolhida que reuniu artesãos de outras comunidades para participarem da “Oficina de Montagem e Desmontagem de Móveis”. O principal objetivo foi ensinar a fabricação de roscas de madeira, para que seus móveis pudessem ser facilmente transportados e montados pelo próprio comprador. Fui convidado para aplicar esta oficina, e após o seu preparo parti para Amazônia paraense.
Neste artigo descrevo o desenvolvimento desta oficina e demais experiências junto a este grupo, que promoveu tantas horas prazerosas de trabalho e aprendizagem.
Por que roscas de madeira?
Um antigo desejo das OCT é tornar prática a montagem de seus móveis, simplesmente rosqueando suas peças. Com este propósito, o treinamento foi dividido em duas partes: a primeira, ensinar a fabricação das rosqueadeiras. Reproduzir esta antiga tecnologia seria uma vantagem, por ser barata e possível de se construir com ferramentas simples, sobras de madeira e sucata. Outra vantagem seria a possibilidade de replicar a ferramenta, havendo esta necessidade. Assim, diferentes diâmetros de rosca podem ser fabricados.
A segunda parte foi ensinar a aplicação da rosca, como um dispositivo de montagem independente, pois não convém fazer a rosca externa na própria perna de um banco ou de uma mesa. No entanto, na oficina de Surucuá ainda se faz necessário cuidar de questões técnicas que antecedem a perfeita confecção destas peças, como a secagem adequada das madeiras e a utilização de um torno, improvisado durante esta oficina com uma furadeira elétrica. As madeiras empregadas normalmente são duras, de difícil secagem, tornando-se estáveis somente após meses ou anos de secagem natural. A madeira úmida ocasiona diversos defeitos como descolagens, rachaduras e folgas de encaixe.
O mobiliário indígena
Segundo Tilde Canti, autor do livro “O Móvel no Brasil – Origens, Evolução e Características” (ed. CGPM, 1985),
“ As diversas tribos aqui encontradas apresentavam diferentes estágios de civilização. Algumas, ainda nômades, viviam ao relento, dormindo sobre folhas, e outras ao sul conheciam a técnica da tecelagem, e dormiam em camas semelhantes à cama europeia. Mas observou-se que a rede, como cama, era utilizada pela maioria das tribos que conheciam a técnica da tecelagem.”
“Os bancos também são frequentes, e se apresentam de vários tipos, desde os toros feitos de assento aos bancos trabalhados em uma só peça de madeira, com decoração geométrica em vermelho ou preto, alguns em forma de animal. Em certas tribos esta peça era privilégio dos homens, em outras tribos privilégio do chefe ou reservados unicamente ao cacique. Bancos de finalidade religiosa também foram utilizados por diversas tribos.” (prancha XXII – Bancos Indígenas. Figs. 1 e 2 – bancos em forma de animais (pássaros), do Alto Xingu. Fig. 3 – desenho do assento do banco 1, em branco e preto. Fig. 4 – banco em forma de animal, Posto Louzada, Alto Xingu. Pg. 75).
O mobiliário das Oficinas Caboclas do Tapajós evoca estas origens, conformando um estilo próprio. Seu principal processo de fabricação é o entalhe, sendo a antiga enxó uma das principais ferramentas utilizadas.
Confeccionando as rosqueadeiras
De acordo com as técnicas comentadas no artigo anterior (onde as descrevo com maiores detalhes), iniciamos nosso trabalho fabricando a rosqueadeira interna (macho), com um parafuso de 1″ de diâmetro e oito fios por polegada. Em alternativa à esmerilhadeira, utilizamos serra de arco e lima triangular para abrir os cortes.
Em seguida aconfeccionamos a faca da rosqueadeira externa (cossinete) com um pedaço de lima velha destemperada, também com serra de arco e lima triangular. Com um maçarico a gás prosseguimos com a têmpera, utilizando água para refrigeração.
Para revenir o metal limpamos a peça e a aquecemos até a cor violeta cobrir seu gume. Concluimos esta etapa com sua afiação.
Com o macho e a faca do cossinete prontos, iniciamos a confecção da caixa do cossinete. Escolhemos um cepo de sucupira amarela, madeira extremamente dura, e utilizando serra de costa e plaina manual retificamos esta peça.
Perfuramos a caixa, abrimos a rosca e a entalhamos para acomodar a faca em seu interior. Para fixar o cepo no banco utilizamos um antigo barrilete.
Tampamos o cossinete, ajustamos a posição correta da faca e o testamos.Utilizamos apenas uma raspilha para o acabamento. Durante a semana foram fabricados vários jogos de rosqueadeiras, para que fossem utilizados e replicados em cada comunidade.
Para fabricar a rosca é necessário um roliço de 1″ e madeira que se preste para este serviço, como a Itaúba – conforme comentado no artigo anterior. Nesta região faz-se quase tudo com Itaúba e suas variedades, das embarcações às casas. É madeira quase incorruptível e comum no Pará. Então, com uma furadeira elétrica e algumas sobras de madeira montamos um torno; entalhamos o roliço e os pinos das roscas, para fixá-los nas extremidades dos pés de um banco de cumarú confeccionado especialmente para este fim.
Com os dispositivos de montagem prontos, preparamos os pés do banco, perfurando suas extremidades.
Abrimos a rosca interna no assento do banco, e nos pés fixamos cada rosca com cola PVA e um contra-pino de madeira como reforço. Neste momento, após cinco dias de atividades, concluimos o nosso treinamento.
O Boto e o Tracajá
Paralelo a este treinamento, acompanhei na oficina a confecção de dois bancos zoomorfos, um em forma de Boto e outro em forma de Tracajá – uma espécie de cágado, comum na região amazônica.
Após a marcação a peça é perfurada – neste caso, para a confecção do banco Boto foi utilizada uma “costaneira”, parte externa do tronco da árvore. Estes furos servem para conduzir o corte com a motosserra.
Com muita habilidade as sobras são separadas, apenas com a ponta da motosserra. Em Surucuá a motosserra é uma ferramenta fundamental em todos os serviços, inclusive nos serviços de oficina. As ferramentas elétricas são alimentadas por um gerador a gasolina.
Com os recortes preliminares prontos, a peça é levada ao banco e entalhada com enxó, formão e goiva. O trabalho é feito por diversas mãos.
Com uma lixadeira de disco elétrica, lixas manuais e raspadores o trabalho de modelagem é finalizado. É interessante notar os belos efeitos causados pela combinação do cerne e do alburno no assento. O acabamento é feito com seladora de nitrocelulose.
Seguindo o mesmo processo de fabricação o banco Tracajá também é confeccionado. Os pés de ambos os bancos são entalhados com enxó.
O banco Tracajá (de sucupira amarela) troquei pelo jogo de rosqueadeiras que levei para esta oficina. Foi um excelente negócio!
Coleta de madeira
No último dia desta semana de trabalho fomos à floresta coletar madeira. Próxima às margens do rio Tapajós a floresta é de várzea, onde ocorrem enchentes periodicamente. Não muito distante da comunidade fomos beneficiar e coletar peças de sucupira amarela, de uma árvore derrubada há algum tempo.
Depois de acomodar o tronco, a marcação é feita com um barbante embebido em óleo queimado. Serão retirados pranchões deste tronco, peças com aproximadamente 70mm de espessura.
As peças são marcadas novamente, e o alburno é retirado. Para os cortes longitudinais é utilizada uma correia apropriada.
Além de beneficiar os troncos de sucupira, derrubamos este cumarú com raízes em forma de sapopema. Para o abate, a correia da motosserra é trocada pela correia de cortes transversais. Derrubar uma árvore deste porte é perigoso, além de poder danificar árvores vizinhas. O corte é feito lentamente, até se ouvir os primeiros estalos; então nos afastamos e esperamos a árvore cair.
Então as peças foram transportadas até a oficina, onde permanecerão secando. São “tabicadas” – separadas por tabiques, ou réguas – para haver ventilação e evitar o apodrecimento.
Destas madeiras serão confeccionados diversos móveis, conferindo uma importante fonte de renda para a comunidade e a divulgação deste belíssimo trabalho, genuinamente brasileiro.
Agradeço aos homens que participaram desta Oficina, conhecedores dos segredos da floresta e que muito me ensinaram.
Aos responsáveis diretos por esta realização: a antropóloga Luciana Carvalho e seu marido Alexandre Nazareth, amigo de muitos anos que retirou-me de minha modesta oficina e trouxe-me para a imensidão da floresta amazônica.
– Diego de Assis
ATENÇÃO
Diversos procedimentos de oficina oferecem riscos. Por isso devem acompanhar o uso de EPI (Equipamento de Proteção Individual): óculos de proteção, máscara contra pó, protetores auriculares, entre outros dispositivos de segurança. Apenas pessoas capacitadas devem operar máquinas e ferramentas de corte; ao contrário estarão sujeitas a acidentes graves.
Filed under: Sem categoria | Leave a Comment
Roscas de madeira
Cossinete arquivo PDF
Para se fazer roscas de madeira é necessário utilizar basicamente um jogo de ferramentas: o cossinete, para fazer a rosca externa, e o macho, para fazer a rosca interna. No mercado brasileiro, até este momento, existe rosqueadeiras manuais apenas para metais ou tubos de PVC, impróprios para madeira. Em minha experiência utilizei diversas ferramentas alternativas, mas nenhum resultado foi satisfatório. Os cossinetes para metal fazem uma rosca frágil e quebradiça na madeira, embora o macho para abrir a rosca funcione bem. Utilizar uma porca comum como um cossinete parece uma boa alternativa, a exemplo de alguns vídeos vistos na Internet, mas não são práticos como parecem.
Então, de acordo com as antigas técnicas de construção, recorri aos mestres, entre os principais Roy Underhill, que além de seus fantásticos vídeos, descreve em seu livro The Woodrigths Workbook a construção e os segredos destas ferramentas. Outra fonte importante está no livro Le Menuisier Ébaniste, de André Roubo, que possui uma perfeita descrição das rosqueadeiras, acompanhada de uma belíssima gravura, cuja edição data do ano de 1774. E, para compreender os segredos da têmpera dos metais, Alexander Weygers, em seu livro The Complete Modern Blacksmith, ensina como tornar o metal resistente e tenaz, através de técnicas simples e acessíveis.
Com estas e demais referências comento, neste artigo, as técnicas de fabricação das rosqueadeiras manuais, como alternativa barata, feita com sucata e sobras de madeira, tão eficientes como as que se faziam há séculos atrás.
Primeira ferramenta: o “macho”
Para abrir a rosca do cossinete, o macho deve estar pronto. Foi feito com um parafuso ordinário de 1”de diâmetro, de oito fios por polegada, rapidamente usinado com esmerilhadeira.
Primeiro o parafuso foi envolvido com fita crepe e marcado com caneta hidrocor. Para um melhor desempenho desta rosqueadeira, estes rasgos foram abertos com ligeira inclinação, no sentido do corte, conforme mostra a imagem seguinte.
Depois, para retirar as rebarbas do metal, o parafuso foi lixado manualmente, abraçado com uma folha de lixa fina para metal, no sentido inverso ao aperto – para “cegar” a ferramenta de um lado e afiar do outro. Assim, quando o macho é retirado, a rosca fica mais preservada.
Atravessei a cabeça do parafuso com uma haste, conformando um punho próprio. Para perfurar o metal é necessário banhar a peça com óleo, o que resfria e evita o desgaste da broca.
O cossinete: modelando a faca
Dentro da pequena caixa de madeira fica alojada a faca em forma de “V”, um pequeno bite que entalha a rosca, transformando um roliço num parafuso. Esta faca deve ser de aço carbono, para poder receber a têmpera e adquirir a resistência necessária para se fazer um gume. Aços com baixo teor de carbono não são capazes de receber a têmpera, embora possam ser cementados com a aplicação superficial de carbono.
Utilizei um pedaço de uma lima velha. As limas são feitas de um aço muito bom, com alto teor de carbono, e se prestam para diversas ferramentas de corte, como goivas e formões. Existem diversas sucatas com alto teor de carbono que podem ser utilizadas, mas como medir este teor?
Um teste rápido é esmerilhar o metal e observar suas faíscas. Um aço com alto teor de carbono expele muita faísca, bastando tocar o esmeril para haver uma “explosão” . Ao contrário, um aço com baixo teor de carbono expele poucas faíscas. Nas imagens comparo um parafuso ordinário com baixo teor de carbono com a peça proveniente da lima velha.
Outro teste é aquecer o metal até o ponto não magnético (rubro), banhar imediatamente a peça em óleo ou água e tentar utilizar uma lima sobre a peça. Se, após o endurecimento do metal a lima deslizar, como se estivesse passando sobre vidro, é sinal que o metal possui alto teor de carbono, por isso pode ser temperado. Para saber se o metal está no ponto não magnético, basta encostar um ímã enquanto o metal ainda estiver rubro. Neste ponto o metal perde atração.
Então, num forno improvisado de tijolos expus o metal ao fogo até enrubescer, ao ponto não magnético. Deixei a peça esfriar naturalmente; assim o metal “relaxa”, permitindo ser facilmente trabalhado.
Para abrir a faca em forma de “V”, fixo a peça na morsa e começo com um ligeiro corte que irá conduzir a lima triangular. Após este corte, a peça é usinada na parte externa, até chegar em sua forma. É interessante notar que o metal está muito maleável, sendo impossível fazer um fio.
A têmpera – endurecendo o metal
Com a peça modelada, preparo o maçarico e a aqueço novamente até o ponto não magnético, rubro, resfriando-a imediatamente em água. Nesta experiência utilizei água sem problemas. Também é recomendado utilizar óleo, pois o resfriamento causa um choque térmico mais “suave”, e o interior do metal se torna menos rígido – e por isso torna o metal mais tenaz.
A água pode eventualmente criar fissuras, se a estrutura do metal não suportar o choque térmico. Neste momento o metal está duro e quebradiço como o vidro, e sujo de escória.
A têmpera – revenindo o metal
O passo seguinte é polir o metal, para que o espectro de cores seja visível durante a têmpera. Após o polimento retornei a peça ao fogo, mas de forma controlada, atento ao espectro que se formaria à medida do aquecimento. O fogo deve tocar a parte oposta ao gume, de forma que o espectro ”caminhe” até o gume. O recozimento – ou revenido – deixará o metal duro o suficiente para receber um fio. “Relaxamos” um pouco o metal desta forma. Esta parte é a mais delicada, pois se passar da cor desejada todo o processo precisa ser refeito.
O espectro de cores indica a temperatura aproximada: a temperatura mais alta é a que está mais próxima da chama, na cor azul-escuro, a mais ou menos 640°C. Cada cor do espectro corresponde a uma dureza específica para o aço. No caso da faca do cossinete, deixei aproximar o gume da faca na cor quase púrpura (peacock), na ordem dos 540°C. Esta é a cor recomendada para as ferramentas de corte delicado, como pequenas goivas. No momento que esta cor chegou ao gume, resfriei a peça rapidamente na água. Agora a faca está pronta para receber o fio.
É certo que para o domínio da têmpera dos metais através desta técnica rudimentar é preciso experiência e muita observação. Como comenta Alexander Weigers, do livro The Complete Modern Blacksmith,”… a vantagem de quem constrói ferramentas é saber que a próxima será ainda melhor!”
A caixa do cossinete
De acordo com as dimensões dadas no livro Le Menuisier Ébaniste, fiz um desenho simplificado, dispensando alguns detalhes, como os punhos torneados e o ornamental orifício de entrada de material.
O parafuso que utilizei contém oito fios por polegada – o que representa, para parafusos de metal, um passe grosso (passe é a distância entre as cristas de um parafuso). Para parafusos que exijam muita tração e movimentos constantes – como o parafuso de uma morsa de bancada -, é necessário uma rosca bem grossa, com passes distantes. Existe uma variedade de passes, mas é preferível passes grossos para parafusos de madeira, por serem mais resistentes.
As madeiras utilizadas devem ser preferencialmente duras, pois uma madeira macia pode perder a rosca. Madeiras como Jatobá, Tauari, Peroba-de-campos, Ipê e Roxinho são madeiras ótimas para confecção da caixa do cossinete. Destas utilizei o Jatobá (Hymenaea courbaril), madeira dura e muito versátil.
A caixa possui uma tampa, que guarda a faca e conduz o roliço no início do corte. Depois de aparelhar a peça, a tampa é separada. As partes são unidas por parafusos em diagonal (o desalinhamento dos parafusos evita que a madeira rache). Após esta fixação, é feito o furo na tampa, com broca chata, pua ou Forstner, controlando sua excursão com uma fita enrolada na broca (utilizei neste caso uma broca chata de 1”). A broca deve ultrapassar ligeiramente a tampa, perfurando o início da caixa. Em seguida a broca é trocada por uma menor, de 7/8”, para perfurar a caixa até atravessá-la. A relação entre os furos é exatamente esta: 1/8 entre as brocas que se vai utilizar.
Após a perfuração é aberta a rosca. Melhor passar antes um pouco de vaselina sólida no furo.
Feita a rosca no cossinete, o próximo passo é marcar a peça e localizar o momento exato para encaixar a faca. A faca pode ser acomodada com o auxílio do próprio macho, encaixando seu gume em sua rosca. Se por acaso a faca ficar mau posicionada, pode ser regulada com os parafusos que a fixam. No desenho de André Roubo, sugere-se utilizar três parafusos, mas nesta experiência achei necessário apenas dois. Roy Underhill sugere uma forma melhor, que é utilizar um parafuso em forma de “L” (escápula), cujo aperto faz-se na parte externa da caixa.
Com a faca fixada a ferramenta é testada e regulada. A tampa recebe os furos para encaixar a cabeça dos parafusos da faca.
Por último os cortes curvos são feitos na serra de fita (opcional), a caixa é lixada e suas arestas retiradas. Ferramentas prontas, vamos à sua utilização.
Dispositivo de fixação
Entre algumas espécies de madeira que experimentei para abrir rosca, a que apresentou melhor resistência ao corte foi a Itaúba preta (Mezilaurus itauba). Acredito que suas primas da família Lauraceae, como as imbuias, louros e canelas também sejam boas madeiras para este propósito.
Uma boa opção é utilizar roscas avulsas, que podem ser aplicadas em praticamente qualquer espécie de madeira. Este parafuso contém uma parte lisa, a cavilha, que é fixada com cola.
Para sua fabricação, após abrir a rosca num roliço, este deve retornar ao torno para desbastar as cavilhas. Num pequeno roliço se produz várias peças.
Desta forma a montagem e desmontagem de móveis, brinquedos e utensílios pode ser prática e segura. Para quem quiser construir o seu próprio cossinete, baixe o arquivo PDF no início do artigo. Bom trabalho!
– Diego de Assis
ATENÇÃO
Diversos procedimentos de oficina oferecem riscos. Por isso devem acompanhar o uso de EPI (Equipamento de Proteção Individual): óculos de proteção, máscara contra pó, protetores auriculares, entre outros dispositivos de segurança. Apenas pessoas capacitadas devem operar máquinas e ferramentas de corte; ao contrário estarão sujeitas a acidentes graves.
Filed under: Sem categoria | 2 Comments
na Finlândia brasileira
Às margens da rodovia Presidente Dutra no Rio de Janeiro situa-se Penedo, distrito de Itatiaia. Local turístico, é representante da cultura finlandesa e está localizada numa das reservas naturais mais exuberantes de nossa mata atlântica.
Nascia em 1929 uma pequena colônia nesta região, fundada e idealizada por Toivo Uuskallio, finlandês filho de artesão; seu pai fabricava móveis, armas e “Kantele”, um instrumento de cordas típico da Finlândia (próxima foto). Toivo pretendia encontrar nos trópicos um clima que permitisse um estilo de vida mais natural, fazendo parte de seu projeto a alimentação vegetariana e a abstenção de bebidas alcoólicas.
Esteve pela primeira vez no Brasil em 1927 e retornou em 1929, após larga divulgação de seu movimento na Finlândia – o que trouxe cerca de 300 finlandeses até 1940. Toivo então compra a Fazenda Penedo, dando início ao desenvolvimento de seus ideais. Hoje Penedo tem por vocação principal o turismo, oferecendo pousadas, restaurantes, artesanatos diversos e passeios pelas trilhas do Parque Nacional do Itatiaia.
Estive em Penedo com minha esposa em dezembro de 2009. Nos dias que sucederam nossa viagem busquei, inquietamente, um roteiro próprio, atrás das coisas de madeira que Penedo escondia em seus primórdios, no artesanato de origem finlandesa (tão peculiar em sua cultura), à parte o circuito do consumo de souvenirs e outros produtos que oferecem em suas lojas. Durante o curto período de uma semana estivemos na “trilha” de pessoas formidáveis que nos ajudaram a compor esta história, visitando suas oficinas e desvendando seus segredos.
Este artigo apresenta um breve resumo deste passeio na “nossa” Finlândia brasileira, um tanto injusto por sua redução, comparado às impressões que tivemos nestes lugares.
Martti Vartia
No restaurante Koskenkorva conhecemos o escultor finlandês Martti Vartia, também proprietário. Considerei esta ocasião o início deste roteiro, deslumbrado por dezenas de esculturas em madeira distribuidas pelo restaurante, entalhadas em raízes e troncos encontrados na região.
É um trabalho realizado a partir da combinação do entalhe com elementos da natureza; surgem criaturas, como se lá já estivessem. Martti as descobre.
Martti mudou-se para o Brasil há mais de trinta anos, vinte e cinco destes morando no Rio de Janeiro. Começou seu trabalho como escultor após sua mudança para Penedo, há nove anos. Por isto talvez seja mais correto referir-se a Martti como um artista brasileiro de origem finlandesa, absolutamente adaptado em nossa cultura e natureza.
Sua oficina é composta de ferramentas manuais simples, como goivas, formões e lixas. De fato, suas ferramentas principais são as suas próprias mãos.
Após longa conversa com forte sotaque finlandês recebemos várias dicas sobre outras coisas de madeira a visitar…
Timo Aaltonen
Foi na pousada Arboretum – a primeira pousada formal da região – que seus proprietários, o simpático casal Otávio e Vanessa Miranda contactaram seu amigo Timo Aaltonen para visitarmos sua oficina. Com sorte Timo e sua esposa Eliana, que dividem sua vida entre Rio e São Paulo, estavam presentes e nos recepcionaram. Um privilégio.
Timo Aaltonen é o autor do livro Sauna Finlandesa (Ed. Edicon), o único do gênero na língua portuguesa. Finlandês, veio para o Brasil com apenas seis anos de idade. É engenheiro de formação, e nas horas vagas um artesão extremamente habilidoso, não havendo em seu trabalho lugar para imprecisões. Pratica marcenaria, carpintaria, entalhe; construiu sua casa, sua sauna, móveis e é um importante colaborador do Museu Finlandês, sendo o autor do busto de Toivo Uuskallio (primeira foto do artigo) e do próprio balcão da recepção (próxima foto).
Sua oficina contém uma diversidade enorme de ferramentas manuais, de formões usinados e temperados por ele mesmo, e entre as máquinas estacionárias uma chamou a atenção; sua serra de fita, toda feita de madeira, funcionando perfeitamente. Timo comenta:
“Esta serra de fita foi feita pelo meu grande mestre e vizinho já falecido, o Johan Faulstich, conhecido como João Alemão, um gênio da artesania”.
Sobre a bancada (construída pelo próprio Timo) uma Swedish Carving Axe, um tipo de machadinha própria para o entalhe artístico, usada em suas esculturas. Belíssima ferramenta, feita pelo artesão Lennart Pettersson, representado na foto do livro The Axe Book.
Uma de suas dicas foi visitarmos a oficina de seu amigo Cláudio José de Souza, um dos marceneiros mais requisitados da região de Penedo. Então, no dia seguinte…
Cláudio José de Souza
Em Penedo seu trabalho é notável, na marcenaria dos restaurantes e na carpintaria das pousadas. Cláudio e demais marceneiros que trabalham em seu galpão praticamente abastecem o distrito e regiões vizinhas.
É mineiro legítimo, e extremamente generoso. Foram horas de conversa sobre seu trabalho, sobre madeiras, ferramentas e personagens locais. Trabalha com madeira desde 1974, e aprendeu através de mestres severos, que não perdoavam erros. Como marceneiro e carpinteiro é rápido e preciso, e reproduz móveis com perfeição. É versátil, utiliza madeiras maciças, compósitos e ferramentas estacionárias e manuais diversas.
Entre as estacionários destacou-se em sua oficina uma antiga serra de fita belga, da marca Danckaert. Segundo Cláudio esta máquina funcionava originalmente com roda d’água. Seu volante possui 1 metro de diâmetro, e aceita fita de até duas polegadas de largura. Uma gigante.
Uma peça curiosa: este gabarito para abrir caixas na furadeira horizontal. Sobre a peça fixa-se os montantes, onde é feita a perfuração para venezianas de paleta americana. Uma peça tão estética quanto funcional.
Ganhei nesta visita duas plainas de cepo – uma de afagar e um guilherme. Não é preciso dizer o quanto fiquei contente com estes presentes…
Museu Finlandês
Foi no Museu Finlandês da Dona Eva que encontramos uma grande coleção de artesanatos típicos, representando a história e a cultura finlandesa de toda a região deste país. À parte, é impressionante o artesanato de madeira, principalmente feito com madeira de bétula, onde se aproveita desde a casca ao cerne.
PUU – Madeira (texto extraído de uma vitrine do museu)
“Os objetos de madeira são fabricados na Finlândia desde a antiguidade. A madeira da árvore bétula (KOIVU) era usado para objetos decorados com perfurações. O abeto (KUUSI) era usado para objetos maiores. O junípero (KATAJA) era usado para canecas e vasilhames diversos. No final da idade média começou o uso do torno para trabalhar a madeira e aumentou a produção de objetos para o lar.”
“Uma casa finlandesa possuia cerca de 50 objetos diferentes de madeira, tais como canecas para água e cerveja, pratos, travessas, baldes, bacias, vasilhas para manteiga e creme de leite, colheres, conchas, facas, rolos de pastel, cantil para água e outros objetos para cozinha.”
“Com o início da indústria de porcelana os objetos de madeira foram sendo substituídos, mas os finlandeses ainda apreciam e usam objetos de madeira, especialemtne na sauna, onde uma caneca de madeira é usada para jogar água nas pedras, e nas casas de campo onde usam as canecas para água e cerveja e facas de madeira para passar manteiga no pão.”
“Os artistas modernos não esqueceram a madeira. A Finlândia produz objetos variados de madeira, tais como enfeites, brinquedos, bijuterias, alguns exemplos dos quais podem ser vistos aqui no museu. Também temos objetos antigos de madeira, usados pelos finlandeses no passado.”
Na foto seguinte o “Cuco da Carélia”, esculpido com faca em um único pedaço de madeira.
“A madeira também é usada para construção de móveis e casas. A Finlândia é uma grande produtora e exportadora de casas pré-fabricadas de madeira.”
“Outra grande aplicação da madeira é a fabricação de celulose e papel, importante produto de exportação da Finlândia. A celulose finlandesa é fabricada a partir dos abetos e pinheiros que permitem a produção de celulose de fibra longa de excelente qualidade para fabricação de papéis especiais, como o papel vegetal usado na engenharia, papéis para revistas e belíssimos guardanapos, papéis especiais para filtros e muitos outros.”
Esta pequena faca é típica para o trabalho em madeira, entre outras utilidades. Sua bainha e sua lâmina são ricamente ornamentadas.
A Finlândia possui também enorme tradição na tecelagem. Entre outras coisas de madeira as rocas e os teares tradicionais representam um antigo e sofisticado trabalho em madeira, na construção de máquinas para a produção de fios e tecidos.
Esta roca mostra um fino trabalho de tornearia, certamente uma das peças mais belas do museu.
Em Penedo a tecelagem é continuada por diversos artesãos, mas principalmente representada pela finlandesa Eila Ampula (1916 – 1996), uma grande artista da tecelagem. Seus trabalhos são encontrados em toda Penedo, além de influenciar o trabalho de outros artesãos.
Estes Pescadores, de Eila Ampula, faz parte do acervo de Martti Vartia.
No atelier Kielo
Kielo é uma típica flor da Finlândia, símbolo deste país. Em Penedo também é o nome do atelier de Rodrigo, O Tecelão – um artesão completo em seu ofício. Rodrigo construiu o seu primeiro tear há 25 anos, no qual tece até hoje, e também possui uma bela coleção destas máquinas em seu atelier, todas em funcionamento.
Na foto o detalhe em madeira entalhada de um tear alemão.
O tear seguinte, construido por Rodrigo, foi feito aos moldes do tear típico finlandês. De ipê e aroeira, madeiras duras e extremamente resistentes.
De todas as rocas que já vi esta é a mais arrojada, a mais moderna. Alguma semelhança com o exemplar do museu?…
Do fio da roca ao tecido do tear – um sistema pleno de artesania.
Segundo Rodrigo, este tear – o maior entre os de sua coleção – é uma versão moderna dos teares suecos e portugueses. Seu design influenciou a construção dos teares mineiros no período colonial.
Com o nosso tempo esgotado fizemos desta a última mostra das coisas de madeira em Penedo. Foi pouco; ficou a sensação de apresentar apenas um indício, entre muitas histórias e segredos que este lugar ainda tem a oferecer.
Agradeço aos que generosamente se dispuseram para a construção deste artigo. Ao Museu Finlandês da Dona Eva, pelo seu precioso acervo.
– Diego de Assis
ATENÇÃO
Diversos procedimentos de oficina oferecem riscos. Por isso devem acompanhar o uso de EPI (Equipamento de Proteção Individual): óculos de proteção, máscara contra pó, protetores auriculares, entre outros dispositivos de segurança. Apenas pessoas capacitadas devem operar máquinas e ferramentas de corte; ao contrário estarão sujeitas a acidentes graves.
Filed under: 1 | 1 Comment
Recent Entries
Categorias
- 1 (10)